
The investigation revealed that all the three designs of Low Modulus (LM) spar, High Modulus (HM) spar and Ultra Modulus (UM) spar failed at 16,801.8 N/m 2 which is above the wing bending moment with ultra-modulus spar having the least deflection of 0.143 m because of its high stiffness property. To carry out progressive failure analyses of the various graphite-epoxy composite wing spar designs under bending moment, finite element analysis with ANSYS 14 Mechanical APDL software was employed to determine which spar design would best withstand the bending moment of 10,000Nm generated from the MATLAB MuPAD software.
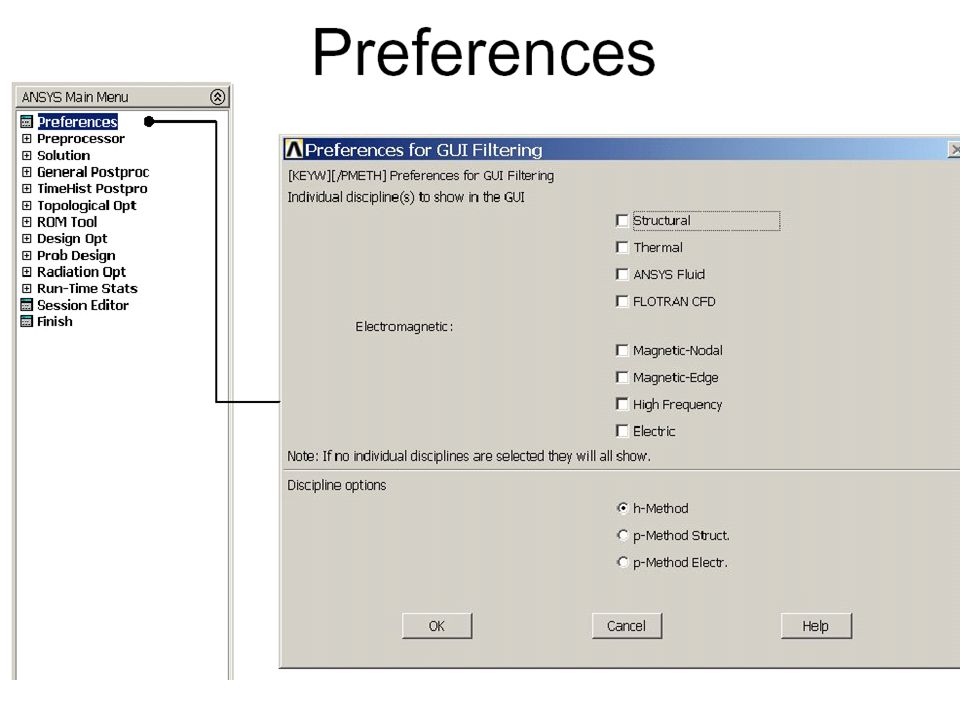
MATLAB MuPAD software was used to derive analytical models for the aircraft wing loads using symbolic computation to estimate shear and bending moment forces acting on the wings while ANSYS 14 Mechanical APDL software was used to design and analyze the modeled composite structures of the wing spar. The adoption of an innovative and lightweight plastic housing for its steering system supports both the ecological and economical goals of thyssenkrupp Presta and helps the company lead the evolution of the steering systems for the automotive market of tomorrow.This research work investigates graphite-epoxy design for light weight high performance structure of an aircraft wing spar using computational techniques. Ansys Mechanical’s short fiber reinforced composite workflow helped thyssenkrupp Presta reach the targeted 50% weight reduction with respect to the original metal part to meet mechanical performance and OEMs requirements. Thyssenkrupp Presta is leveraging its longstanding competencies in materials, components and systems to lead automotive digital transformation processes. Chapter 7: Generating Mesh - I Chapter 8: Generating Mesh II Chapter 9: Static Structural Analysis Chapter 10: Modal Analysis Chapter 11: Thermal Analysis Index Finite Element Simulations with ANSYS Workbench 15 is a comprehensive and easy to understand workbook. For the high-volume production models (body panels, frames, housings), an increasingly adopted technique is the manufacturing of critical components through injection molding with short-fiber reinforced plastics. Composite materials are key to making vehicles lighter so they can use smaller engines that consume less energy and produce fewer emissions.

To do so, leading vehicle manufactures and their partners are embracing lightweighting and electrification.

In the automotive industry, there is a global push to reach zero vehicle emissions by 2050 to satisfy consumer demand and increasingly stricter environmental laws. All products have an environmental impact, a fact customers are increasingly aware of as they take an interest in their carbon footprints.
